Magnetic Flux Leakage (MFL)

Magnetic Flux Leakage (MFL) uses a powerful magnet to magnetize the conductive material under test (usually steel). Where there are defects — corrosion or material loss — the magnetic field “leaks” from the steel.
MFL probes incorporate a magnetic detector placed between the poles of the magnet where it can detect the leakage field. During inspection, a magnetic circuit of sorts forms between the part and the probe. The magnetic field induced in the part saturates it until it can no longer hold any more flux. The flux overflows and leaks out of the pipe wall and strategically placed sensors can accurately measure the three-dimensional vector of the leakage field.
As with MPI, the ferromagnetic specimen is magnetised by one of the methods listed, and depending upon the level of induced flux density, magnetic flux leakage due to both near- and far-surface flaws is detected by the voltage induced in a detector coil or a Hall effect element, which is traversed over the surface of the specimen. Unlike MPI, the method is not limited to surface-breaking or near-surface flaws, but actually becomes increasingly sensitive to far-surface flaws with increasing levels of magnetisation. Also, the output from the detector can be amplified, filtered, digitised, etc and stored to produce automated inspection systems. The method is widely used on bar and tube stock with both rotating specimens and rotating probes. Multi-element and differential probes are also used, and inspection speeds can be very high. One technique, known as magnetography, utilises a special form of magnetic tape applied to the surface of a specimen during magnetisation, allowing flux leakage fields to be picked up and stored on the tape. The tape can then be removed from the specimen for processing and analysis of the signals.
The method is also finding increasing use in the petrochemical industries for providing high-speed inspections of storage tank floors, as well as carbon steel pipes. These systems utilise either permanent or electromagnets to provide localised near-magnetic saturation coupled with induction coil or Hall effect sensor arrays for detecting anomalous flux leakage caused by the presence of corrosion defects (both near and far surface). Many of these systems rely upon the use of an adjustable threshold or amplitude gate to provide the detection of corrosion in real-time, while some of the more advanced systems, through the use of both advanced electronics and signal processing are able to provide corrosion maps of inspected areas similar to the C-scan representation of ultrasonic data.
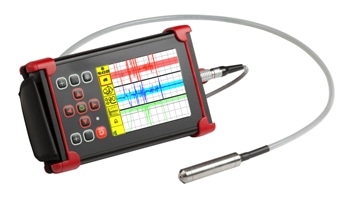